2025-02-28
3D-Laserschneidtechnologie - eine Revolution in der Bearbeitung von Rohren, Profilen und speziellen Formteilen
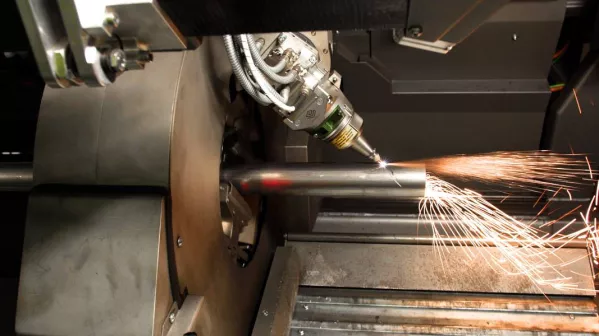
Die 3D-Laserschneidtechnologie hat die Metallbearbeitungsindustrie revolutioniert, indem sie ein neues Maß an Präzision, Flexibilität und Effizienz in der Herstellung von Bauteilen aus Rohren, Profilen und speziellen Formteilen eingeführt hat. Im Gegensatz zu konventionellen mechanischen Methoden ermöglicht diese Technologie die Durchführung komplexer Schneidoperationen ohne den Einsatz mehrerer Werkzeuge und zahlreicher Bearbeitungsschritte. Dieser Artikel bietet eine umfassende Analyse der 3D-Laserschneidtechnologie, ihrer Funktionsprinzipien, der verwendeten Lasertypen sowie der technischen Schlüsselaspekte dieser innovativen Bearbeitungsmethode.
Funktionsprinzipien von 3D-Laserschneidmaschinen
Physikalische Grundlagen des Prozesses
Das 3D-Laserschneiden basiert auf der Verwendung eines hoch energetischen, fokussierten Lichtstrahls, der lokal begrenztes Schmelzen, Verbrennen oder Verdampfen des Materials in einem genau definierten Bereich bewirkt. Dieser Prozess initiiert eine thermische Reaktion, bei der Material abgetragen wird und ein präziser Schnittspalt entsteht. Kern der Technologie ist die Möglichkeit, den Laserstrahl dreidimensional zu steuern, was die Bearbeitung räumlicher Objekte wie Rohre oder Profile ermöglicht.
Kinematik von 3D-Laserschneidmaschinen
3D-Laserschneidmaschinen zeichnen sich durch eine komplexe Kinematik aus, die eine präzise Führung des Laserkopfes um das Werkstück herum ermöglicht. Es werden zwei Haupttypen von kinematischen Systemen unterschieden:
Systeme mit bewegtem Laserkopf und Drehtisch:
- Das Werkstück wird um seine Längsachse gedreht
- Der Laserkopf bewegt sich in den X-, Y- und Z-Achsen
- Integrierte Drehsysteme ermöglichen eine zusätzliche Drehachse (B oder C)
- Ermöglicht die Bearbeitung aus beliebigen Richtungen um das Bauteil herum
Systeme mit feststehendem Laserkopf und mehrachsiger Werkstückmanipulation:
- Der Laserkopf bleibt in fester Position
- Das Werkstück wird durch ein System mit mindestens 5 Freiheitsgraden bewegt
- Bietet höhere Präzision bei der Bearbeitung schwerer Bauteile
- Eignet sich besser für die Bearbeitung großer Formteile
Prozesssteuerung
Moderne 3D-Laserschneidsysteme sind mit fortschrittlichen CNC-Steuerungen ausgestattet, die für folgende Aufgaben verantwortlich sind:
- Präzise Positionierung des Laserkopfes relativ zum Profil
- Kontrolle der Laserstrahlparameter (Leistung, Betriebsmodus, Fokus)
- Management des Kühlprozesses
- Synchronisation der Dreh- und Linearachsen
- Adaptive Echtzeit-Prozesskontrolle
Ein Schlüsselelement ist die CAD/CAM-Software, die die Konstruktion komplexer Formen und die automatische Generierung von Werkzeugpfaden ermöglicht. Diese Systeme sind oft mit Schnittprozess-Simulationsmodulen ausgestattet, die potenzielle Kollisionen erkennen und die Bearbeitungsparameter optimieren.
Unterschiede zwischen 2D- und 3D-Laserschneiden
Dimensionskonzept in der Laserbearbeitung
Der grundlegende Unterschied zwischen 2D- und 3D-Systemen betrifft die Anzahl der Achsen, entlang derer sich der Schneidkopf bewegt, sowie die Freiheitsgrade der Werkstückmanipulation:
2D-Systeme:
- Arbeiten in einem zweiachsigen kartesischen Koordinatensystem (X und Y)
- Bestimmt für das Schneiden flacher Materialien (Bleche, Platten)
- Haben typischerweise einen festen Strahlfokus oder eine begrenzte Z-Achsen-Regelung
3D-Systeme:
- Operieren mit mindestens fünf Achsen
- Ermöglichen die Bearbeitung gekrümmter Oberflächen und räumlicher Bauteile
- Bieten die Möglichkeit, den Laserkopf in jedem beliebigen Winkel zur Oberfläche auszurichten
Komplexität der Bearbeitung
Das 3D-Laserschneiden ist durch eine deutlich höhere technologische Komplexität gekennzeichnet:
Spezialanwendungen
Das 3D-Laserschneiden eröffnet neue Möglichkeiten in folgenden Bereichen:
- Herstellung von "Puzzle"-Verbindungen in Rohrkonstruktionen
- Realisierung komplexer technischer und dekorativer Öffnungen
- Präzise Vorbereitung von Bauteilenden für das anschließende Schweißen
- Herstellung von Ausschnitten in Winkeln, die nicht senkrecht zur Profiloberfläche stehen
- Bearbeitung von Bauteilen mit variabler Querschnittsgeometrie
Lasertypen für die Metallbearbeitung
CO₂-Laser
CO₂-Laser verwenden eine Gasmixtur (Kohlendioxid, Stickstoff, Helium) als aktives Medium. Sie erzeugen einen Strahl mit einer Wellenlänge von 10,6 μm, der im Infrarotbereich liegt.
Eigenschaften:
- Leistung: 1,5 kW bis 20 kW
- Energieeffizienz: 8-10%
- Strahlqualität: hoch, besonders bei niedrigeren Leistungen
- Betriebskosten: moderat, hauptsächlich durch Gas- und Spiegelwechsel
Vorteile beim 3D-Schneiden:
- Hervorragende Schnittkantenqualität bei Kohlenstoff- und niedriglegierten Stählen
- Möglichkeit sehr schmaler Schnittfugen
- Gute Absorption durch die meisten Konstruktionsmaterialien
Einschränkungen:
- Geringere Effizienz bei reflektierenden Materialien (Aluminium, Kupfer)
- Notwendigkeit komplexer optischer Systeme mit beweglichen Spiegeln
- Begrenzte Miniaturisierungsmöglichkeiten des optischen Systems
Faserlaser (Fiber)
Faserlaser verwenden mit Seltenen Erden (meist Ytterbium) dotierte Glasfasern als aktives Medium. Sie erzeugen einen Strahl mit einer Wellenlänge von etwa 1,07 μm.
Eigenschaften:
- Leistung: 1 kW bis 30 kW
- Energieeffizienz: 25-35%
- Strahlqualität: sehr hoch, auch bei hohen Leistungen
- Betriebskosten: niedrig, minimaler Wartungsaufwand
Vorteile beim 3D-Schneiden:
- Höhere Absorption durch Metalle, insbesondere reflektierende
- Möglichkeit des Strahltransports über Lichtleiter zum Schneidkopf
- Hervorragende Schneidparameter für dünne Materialien
- Hohe Energieeffizienz
Einschränkungen:
- Höhere Anschaffungskosten
- Größeres Durchschlagrisiko bei Rohren mit kleinen Durchmessern
Scheibenlaser
Scheibenlaser verwenden eine dünne Kristallscheibe (meist Yb:YAG) als aktives Medium. Sie erzeugen einen Strahl mit einer Wellenlänge von etwa 1,03 μm.
Eigenschaften:
- Leistung: 1 kW bis 16 kW
- Energieeffizienz: 15-25%
- Strahlqualität: extrem hoch, unabhängig von der Ausgangsleistung
- Betriebskosten: mittel, höher als bei Faserlasern
Vorteile beim 3D-Schneiden:
- Beste Strahlqualität bei hohen Leistungen
- Hervorragende Energiekonzentration
- Präzise Bearbeitung dickerer Materialien
Einschränkungen:
- Komplexer Aufbau des optischen Systems
- Höhere Anschaffungs- und Wartungskosten
- Geringere Marktverfügbarkeit
Vergleich der Lasertechnologien für 3D-Schneidanwendungen:
Wellenlänge:
- CO₂-Laser: 10,6 μm
- Faserlaser: 1,07 μm
- Scheibenlaser: 1,03 μm
Absorption durch Stahl:
- CO₂-Laser: Gut
- Faserlaser: Sehr gut
- Scheibenlaser: Sehr gut
Absorption durch Aluminium:
- CO₂-Laser: Schwach
- Faserlaser: Gut
- Scheibenlaser: Gut
Maximale Schnittdicke (Stahl):
- CO₂-Laser: 25 mm
- Faserlaser: 30 mm
- Scheibenlaser: 35 mm
Kantenqualität:
- CO₂-Laser: Sehr gut
- Faserlaser: Gut
- Scheibenlaser: Sehr gut
Schnittgeschwindigkeit bei dünnen Materialien:
- CO₂-Laser: Mäßig
- Faserlaser: Hoch
- Scheibenlaser: Hoch
Systemflexibilität:
- CO₂-Laser: Begrenzt
- Faserlaser: Sehr hoch
- Scheibenlaser: Hoch
Anschaffungskosten:
- CO₂-Laser: Niedrig/mittel
- Faserlaser: Mittel/hoch
- Scheibenlaser: Hoch
Betriebskosten:
- CO₂-Laser: Mittel
- Faserlaser: Niedrig
- Scheibenlaser: Mittel
Energiebedarf:
- CO₂-Laser: Hoch
- Faserlaser: Niedrig
- Scheibenlaser: Mittel
Komponenten eines 3D-Laserschneidsystems
Laserquelle
Die Laserquelle bildet das Herz des Systems und ist für die Erzeugung des Strahls mit den erforderlichen Parametern verantwortlich. Wichtige Komponenten sind:
- Laserresonator
- Stromversorgung
- Kühlsystem
- Steuerung der Strahlparameter
- Überwachungs- und Diagnosesysteme
Strahlführungssystem
Abhängig vom Lasertyp wird der Strahl auf folgende Weise zum Schneidkopf transportiert:
- Spiegelsystem (CO₂-Laser) - System präzise ausgerichteter Strahlumlenkspiegel
- Lichtleiter (Faser- und Scheibenlaser) - flexible optische Faser zur Strahlübertragung
Schneidkopf
Ein moderner 3D-Schneidkopf enthält:
- Strahlfokussierung (Linsen oder Spiegel)
- Abstandsregelung zum Material (kapazitiv oder induktiv)
- Düse für den Prozessgaszutritt
- Kühlsystem
- Prozesssensoren (Temperatur, Gasdruck)
- Kollisionsschutzsystem
Positioniersystem
Das Positioniersystem von 3D-Maschinen umfasst:
- Präzise Linearachsenantriebe
- Servomotoren mit Encodern für Drehachsen
- Positionsmesssysteme
- Fortgeschrittene Bewegungssteuerungsalgorithmen
- Kalibrierungs- und Fehlerkompensationssysteme
Steuerungseinheit
Moderne Steuerungssysteme für 3D-Schneidmaschinen zeichnen sich aus durch:
- Industrielle Multicore-Prozessoren
- CAD/CAM-Software
- Kollisionsprädiktionssystem
- Intelligente Werkzeugpfadoptimierungsalgorithmen
- Schnittstellen zur Produktionsmanagementsystem-Kommunikation
Technologischer Prozess des 3D-Laserschneidens
Datenvorbereitung
Der Prozess beginnt mit:
- Erstellung eines 3D-Modells des Bauteils
- Konstruktion der Schnittgeometrien
- Generierung der Werkzeugpfade
- Simulation des Schneidprozesses
- Optimierung der Prozessparameter
Einstellung der Prozessparameter
Wichtige Parameter des 3D-Laserschneidens sind:
- Laserleistung (typisch 1-6 kW für Rohre und Profile)
- Vorschubgeschwindigkeit (üblicherweise 1-10 m/min, abhängig von Material und Dicke)
- Strahlfokussierung (Fokusposition relativ zur Oberfläche)
- Auswahl des Prozessgases (Sauerstoff, Stickstoff, Argon)
- Gasdruck (0,5-20 bar)
- Düsenabstand zum Material (0,5-2,0 mm)
Schneidstrategien
In der 3D-Bearbeitung werden verschiedene Schneidstrategien angewendet:
- Ringförmiges Schneiden - der Schneidkopf bewegt sich um das Profil und führt einen vollständigen Schnitt durch
- Segmentiertes Schneiden - das Profil wird in Abschnitte unterteilt, die sequentiell bearbeitet werden
- Spiralschneiden - der Schneidpfad verläuft spiralförmig um das Profil
- Adaptives Schneiden - Parameter und Pfad werden in Echtzeit angepasst
Qualitätskontrolle
Moderne 3D-Schneidsysteme integrieren fortschrittliche Qualitätskontrollmethoden:
- Adaptive Laserleistungsregelung
- Echtzeit-Prozessüberwachung (Wärmebildkameras, optische Sensoren)
- Systeme zur Fehlererkennung
- Geometrische Messungen der fertigen Bauteile
- Dokumentation der Prozessparameter zur Sicherstellung der Reproduzierbarkeit
Technische Herausforderungen beim 3D-Laserschneiden
Geometrische Präzision
Die Gewährleistung hoher Maßhaltigkeit beim 3D-Schneiden erfordert Lösungen für folgende Probleme:
- Kompensation thermischer Verformungen
- Berücksichtigung der Materialrückfederung nach dem Schneiden
- Minimierung der Schnittfugenkonizität
- Kontrolle der Schnittrechtwinkligkeit zur Oberfläche
Thermische Probleme
Das 3D-Laserschneiden ist mit folgenden thermischen Herausforderungen verbunden:
- Ungleichmäßige Erwärmung von Profilen und Rohren
- Überhitzungsrisiko bei dünnen Wandstärken
- Kontrolle der Wärmeeinflusszone bei empfindlichen Materialien
- Wärmeableitung aus der Schnittzone
Materialbedingte Herausforderungen
Die Vielfalt der in der Profil- und Rohrherstellung verwendeten Materialien führt zu spezifischen Problemen:
- Oberflächenreflexion von Aluminium- und Kupferlegierungen
- Unterschiedliche Energieabsorption verschiedener Materialien
- Probleme beim Schneiden von Verbund- und Mehrschichtmaterialien
- Qualitätskontrolle der Schnittkanten bei Materialien mit unterschiedlicher Struktur
Aktuelle Trends in der 3D-Laserschneidtechnologie
Intelligente Steuerungssysteme
Moderne 3D-Schneidmaschinen sind ausgestattet mit:
- Maschinellen Lernsystemen zur Parameteroptimierung
- Adaptiven Prozessreglern mit Rückkopplungsschleifen
- Prädiktiver Diagnostik
- Operator-Assistenzsystemen basierend auf Augmented Reality
Hochleistungslaser
Die Entwicklung von Laserquellen ermöglicht:
- Bearbeitung von Profilen mit größeren Wandstärken
- Erhöhung der Schnittgeschwindigkeiten
- Verbesserung der Kantenqualität
- Erweiterung des Materialspektrums
Integration in Produktionssysteme
Moderne 3D-Schneidsysteme sind Teil umfassenderer Produktionssysteme:
- Direkte Integration in Produktionsmanagementsysteme
- Automatisierung von Be- und Entladeprozessen
- Synchronisation mit nachfolgenden Bearbeitungsschritten
- Vollständige Rückverfolgbarkeit und Prozessdokumentation
Zusammenfassung
Die 3D-Laserschneidtechnologie stellt einen Durchbruch in der Bearbeitung von Rohren, Profilen und speziellen Formteilen dar. Dank der Möglichkeit präziser räumlicher Bearbeitung ermöglicht sie die Realisierung komplexer Formen und Verbindungen, die zuvor schwierig oder unmöglich herzustellen waren. Die dynamische Entwicklung sowohl der Laserquellen als auch der Steuerungssysteme macht diese Methode immer effizienter, präziser und wirtschaftlicher. Gleichzeitig bestehen weiterhin technische Herausforderungen, insbesondere bei der Bearbeitung reflektierender Materialien und der Prozessqualitätskontrolle, die Gegenstand intensiver Forschung und Entwicklung sind.
«zurück