2025-02-15
Components of Robotic Welding Systems: A Comprehensive Overview
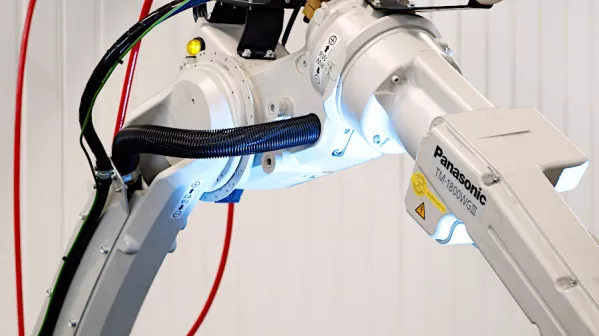
Robotic welding has become a key element of modern manufacturing processes across many industries. The dynamic development of this technology contributes to significant improvements in productivity, quality, and safety in welding operations. At the core of an efficient robotic welding system lies the proper configuration of its components, which together form an integrated, precise, and reliable production station. This article provides a detailed analysis of the main components of robotic welding systems, their technical specifications, and their functional interrelationships.
1. Robotic Arm and Its Characteristics
1.1. Types of Robots Used in Welding
Welding applications primarily use serial-kinematic (anthropomorphic) robots, which are known for their versatility and flexibility. The most common configurations are 6-axis robots, allowing the welding tool to be positioned at any angle within the workspace. In specialized applications, the following types are also used:
- SCARA robots – mainly used for welding flat components
- Parallel-kinematic robots – employed in applications requiring high dynamics
- Gantry robots – dedicated to welding large-scale structures
1.2. Technical Parameters of Welding Robot Arms
Key parameters of welding robots include:
- Payload capacity – typically ranging from 6-210 kg (including the welding torch weight)
- Working range – from 1.4 m for small applications to over 3.5 m for large-scale robots
- Positioning repeatability – within ±0.05-0.1 mm
- Degrees of freedom – most commonly 6-axis, though advanced applications may use 7-axis solutions
- Movement speed – reaching up to 2 m/s for rapid transitions between welding points
- Environmental resistance – protective covers to shield against welding spatter and dust
1.3. Specialized Design Solutions
Robotic welding systems incorporate several specialized design features:
- Internal cable routing (hollow wrist) for power and control wires
- Protective coatings resistant to welding spatter
- Joint cooling systems for high-heat applications
- Reinforced wrist structures ensuring stability during welding
2. Welding Tools
2.1. Welding Torches
Torches are a critical interface between the robot and the welding process. The main types include:
2.1.1. MIG/MAG Torches
- Air-cooled (up to 250-300 A)
- Liquid-cooled (up to 500-600 A)
- Torches with automatic cleaning (TCP – Tool Center Point)
- Torches with integrated sensors (arc voltage, temperature, gas flow)
2.1.2. TIG Torches
- Standard tungsten electrode torches
- Cold wire feed torches
- Quick-change electrode systems
- Specialized high-current torches with cooled electrodes
2.1.3. Laser Welding Heads
- Optical beam-shaping heads
- Hybrid heads (laser + MIG/MAG)
- Scanning heads enabling welding without robot arm movement
2.2. Wire Feeding Systems
Precise and reliable wire feeding is essential for robotic welding. Key components include:
2.2.1. Wire Feeders
- Push feeders – with the feeding mechanism near the wire spool
- Pull feeders – with the feeding mechanism near the torch
- Push-pull systems – ensuring optimal control over long distances
- Servo-driven feeders – providing precise speed control
2.2.2. Wire Spools and Drums
- Standard spools (5-18 kg)
- Large drums (100-300 kg) for mass production
- Quick-change spool systems minimizing downtime
2.2.3. Wire Guides
- Armored guides for different materials (aluminum, steel, special alloys)
- Roller guides for soft materials
- Low-friction guides for flux-cored wires
2.3. Torch Mounting Systems
The method of attaching the torch to the robot arm impacts process precision:
- Rigid mounts for standard applications
- Compliant mounts compensating for positioning inaccuracies
- Quick-change systems (QCS – Quick Change System)
- Anti-collision mounts with built-in protection
3. Control and Programming Systems
3.1. Welding Robot Controllers
Modern welding robot controllers feature:
- Integrated welding process and motion control
- Multi-axis coordination (positioners, linear tracks)
- Advanced path interpolation for complex trajectories
- Safety modules compliant with ISO/TS 15066
- Communication with higher-level systems (MES, ERP)
3.2. Welding Power Sources
Modern welding power supplies for robotic applications offer:
- Digital parameter control at kHz frequencies
- Advanced modes (CMT – Cold Metal Transfer, pulsed, AC MIG)
- Real-time parameter monitoring and logging
- Communication interfaces (EtherNet/IP, Profibus, DeviceNet)
- Adaptive algorithms adjusting to process variations
3.3. Programming Methods
Depending on production needs, different programming techniques are used:
3.3.1. Online Programming
- Teach-in – manually guiding the robot through trajectory points
- Teach pendant programming
- Motion tracking programming
3.3.2. Offline Programming
- CAD/CAM systems with robot path generation
- Simulation environments for pre-deployment verification
- Automated program generation from CAD models
- Path optimization considering accessibility and collisions
3.3.3. Hybrid Systems
- Offline pre-programming with on-site refinement
- Parametric programs adapting to product variants
- Machine learning-based optimization
4. Auxiliary Equipment
4.1. Positioners and Turntables
These optimize welding positioning and ensure quality:
4.1.1. Types of Positioners
- Single-axis rotary tables
- Two-axis L-type positioners
- Three-axis positioners for full orientation control
- Multi-station positioners with part exchange during welding
4.1.2. Technical Parameters
- Payload capacity – from tens of kg up to 20 tons
- Positioning repeatability – ±0.1 mm
- Synchronization with robot movement
- Rotation speeds – typically 10-120°/s
4.2. Linear Tracks and Robot Positioning Systems
For large workspaces:
- Floor-mounted tracks – extending horizontal reach
- Gantry systems – enabling 3-axis positioning
- Column-mounted systems – for tall structures
- Mobile solutions – allowing flexible reconfiguration
4.3. Workpiece Fixturing
Precise and stable clamping is critical for quality:
- Welding jigs with thermal distortion compensation
- Pneumatic/hydraulic clamping for repeatability
- Modular quick-assembly systems
- Fixtures with integrated positioning elements
- Clamping verification (sensors, vision systems)
4.4. Torch Cleaning Systems
For uninterrupted operation:
- Automatic contact tip cleaners
- Spatter removal tools
- Anti-spatter spray systems
- Torch tip geometry inspection
- Wire cutting mechanisms
5. Sensing and Process Monitoring
5.1. Seam Tracking Sensors
Modern robotic welding uses various sensors for adaptive control:
5.1.1. Arc Sensors
- Voltage monitoring during torch oscillation
- Edge detection based on electrical parameter changes
- Adaptive parameter adjustment
5.1.2. Vision Sensors
- Laser scanners for pre-weld geometry
- 2D/3D cameras for real-time seam tracking
- Thermal imaging for temperature monitoring
5.1.3. Touch Sensors
- Part locating via physical contact
- Seam geometry measurement
5.2. Real-Time Quality Control
Advanced systems incorporate:
- Electrical parameter monitoring (voltage, current, arc stability)
- Vision-based weld inspection
- Ultrasonic defect detection
- Process analytics with anomaly detection
6. System Integration
6.1. Robotic Cell Safety
Robotic welding requires comprehensive safety measures:
- Fixed and movable safety barriers
- Light curtains and laser scanners
- Emergency stop systems
- Reduced-speed modes for programming
- Compliance with ISO 10218 and ISO/TS 15066
6.2. Fume Extraction and Filtration
Effective fume management is crucial:
- Local extraction at the torch
- Centralized filtration with heat recovery
- Air quality monitoring
- Material-specific filters
6.3. Integration with Production Systems
Modern robotic welding is part of the digital factory ecosystem:
- MES (Manufacturing Execution System) connectivity
- Quality management system integration
- Big Data analytics
- Industry 4.0 and IoT implementation
- Digital twins for predictive maintenance
Integrated Ecosystem
The components of robotic welding systems form a complex, integrated ecosystem where efficiency depends on proper selection and configuration. Modern solutions are highly digitalized, adaptive, and capable of integration with higher-level production systems. Key development trends include increased autonomy, advanced sensing, AI implementation, and comprehensive quality control. A thorough understanding of each component and their interrelationships is essential for effective design, implementation, and operation of robotic welding systems in modern manufacturing.
«return