2025-02-28
3D Laser Cutting Technology - A Revolution in Processing Tubes, Profiles, and Special Sections
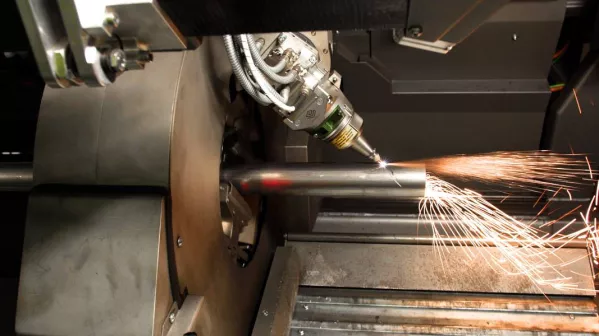
3D laser cutting has revolutionized the metalworking industry by introducing a new level of precision, flexibility, and efficiency in manufacturing components from tubes, profiles, and special sections. Unlike conventional mechanical methods, this technology enables complex cutting operations without the need for multiple tools and numerous machining steps. This article provides a comprehensive analysis of 3D laser cutting technology, its operating principles, types of lasers used, and key technical aspects of this innovative machining method.
Operating Principles of 3D Cutting Machines
Physical Fundamentals of the Process
3D laser cutting relies on the use of a high-energy focused light beam that causes localized melting, burning, or vaporization of the material in a precisely defined area. This process initiates a thermal reaction during which the material is removed, creating a precise cutting kerf. The essence of the technology lies in the ability to manipulate the laser beam in three dimensions, enabling the machining of spatial objects such as tubes or profiles.
Kinematics of 3D Cutting Machines
3D laser cutting machines feature complex kinematics that allow precise guidance of the laser head around the workpiece. There are two main types of kinematic systems:
Systems with a Moving Head and Rotary Table:
- The workpiece is rotated around its longitudinal axis.
- The laser head moves along the X, Y, and Z axes.
- Integrated rotary systems provide an additional rotational axis (B or C).
- Enable machining from any direction around the component.
Systems with a Fixed Head and Multi-Axis Workpiece Manipulator:
- The laser head remains in a fixed position.
- The workpiece is manipulated by a system with at least 5 degrees of freedom.
- Offer greater precision when machining heavy components.
- Better suited for processing large special sections.
Process Control
Modern 3D laser cutting systems are equipped with advanced CNC (Computer Numerical Control) systems responsible for:
- Precise positioning of the cutting head relative to the profile.
- Control of laser beam parameters (power, mode, focus).
- Cooling process management.
- Synchronization of rotary and linear axes.
- Adaptive real-time process control.
A key element is advanced CAD/CAM software, which enables the design of complex shapes and automatic generation of tool paths. These systems often include cutting process simulation modules that allow for collision detection and machining parameter optimization.
Differences Between 2D and 3D Laser Cutting
Dimensionality Concept in Laser Machining
The fundamental difference between 2D and 3D systems lies in the number of axes along which the cutting head moves and the degrees of freedom for workpiece manipulation:
2D Systems:
- Operate in a two-axis Cartesian system (X and Y).
- Designed for cutting flat materials (sheets, plates).
- Typically have a fixed beam focus or limited Z-axis adjustment.
3D Systems:
- Operate in a system of at least five axes.
- Enable machining of curved surfaces and spatial components.
- Allow the cutting head to be positioned at any angle relative to the workpiece surface.
Machining Complexity
3D laser cutting is characterized by significantly greater technological complexity:
Geometric Requirements:
- Continuous control of the nozzle distance from the component surface.
- Maintaining the optimal beam incidence angle on the surface.
- Geometric compensation for curved surfaces.
Process Challenges:
- Variable heat dissipation conditions depending on geometry.
- Need for real-time parameter adaptation.
- Risk of damaging the opposite wall of the profile or tube.
Programming Aspects:
- Complex path generation algorithms.
- Multi-stage process planning.
- Advanced visualization and program verification.
Specialized Applications
3D laser cutting opens new possibilities for:
- Creating "jigsaw"-type joints in tubular structures.
- Producing complex technical and decorative holes.
- Preparing precise component ends for subsequent welding.
- Making cuts at angles other than perpendicular to the profile surface.
- Machining components with variable cross-section geometry.
Types of Lasers Used for Metal Machining
CO₂ Lasers
CO₂ lasers use a gas mixture (carbon dioxide, nitrogen, helium) as the active medium. They generate a beam with a wavelength of 10.6 μm, which falls within the infrared range.
Characteristics:
- Power: 1.5 kW to 20 kW.
- Energy efficiency: 8-10%.
- Beam quality: High, especially at lower powers.
- Operating costs: Moderate, mainly related to gas and mirror replacement.
Advantages in 3D Cutting:
- Excellent edge quality when cutting carbon and low-alloy steels.
- Ability to achieve a narrow cutting kerf.
- Good absorption by most structural materials.
Limitations:
- Lower efficiency when cutting reflective materials (aluminum, copper).
- Need for complex optical systems with moving mirrors.
- Limited potential for optical system miniaturization.
Fiber Lasers
Fiber lasers use glass fibers doped with rare-earth elements (most commonly ytterbium) as the active medium. They generate a beam with a wavelength of approximately 1.07 μm.
Characteristics:
- Power: 1 kW to 30 kW.
- Energy efficiency: 25-35%.
- Beam quality: Very high, maintained even at high powers.
- Operating costs: Low, minimal maintenance required.
Advantages in 3D Cutting:
- Higher absorption by metals, especially reflective ones.
- Ability to transport the beam via fiber optic cable to the cutting head.
- Excellent cutting parameters for thin materials.
- High energy efficiency.
Limitations:
- Higher initial costs.
- Greater risk of breakthrough when cutting small-diameter tubes.
Disk Lasers
Disk lasers use a thin crystalline disk (most commonly Yb:YAG) as the active medium. They generate a beam with a wavelength of approximately 1.03 μm.
Characteristics:
- Power: 1 kW to 16 kW.
- Energy efficiency: 15-25%.
- Beam quality: Extremely high, independent of output power.
- Operating costs: Moderate, higher than fiber lasers.
Advantages in 3D Cutting:
- Highest beam quality at high powers.
- Excellent energy concentration.
- Ability to precisely machine thicker materials.
Limitations:
- Complex optical system design.
- Higher purchase and maintenance costs.
- Lower market availability.
Comparison of Laser Technologies for 3D Cutting Applications:
Wavelength:
- CO₂ Laser: 10.6 μm.
- Fiber Laser: 1.07 μm.
- Disk Laser: 1.03 μm.
Absorption by Steel:
- CO₂ Laser: Good.
- Fiber Laser: Very good.
- Disk Laser: Very good.
Absorption by Aluminum:
- CO₂ Laser: Poor.
- Fiber Laser: Good.
- Disk Laser: Good.
Maximum Cutting Thickness (Steel):
- CO₂ Laser: 25 mm.
- Fiber Laser: 30 mm.
- Disk Laser: 35 mm.
Edge Quality:
- CO₂ Laser: Very good.
- Fiber Laser: Good.
- Disk Laser: Very good.
Cutting Speed for Thin Materials:
- CO₂ Laser: Moderate.
- Fiber Laser: High.
- Disk Laser: High.
System Flexibility:
- CO₂ Laser: Limited.
- Fiber Laser: Very high.
- Disk Laser: High.
Purchase Cost:
- CO₂ Laser: Low/medium.
- Fiber Laser: Medium/high.
- Disk Laser: High.
Operating Costs:
- CO₂ Laser: Moderate.
- Fiber Laser: Low.
- Disk Laser: Moderate.
Energy Consumption:
- CO₂ Laser: High.
- Fiber Laser: Low.
- Disk Laser: Moderate.
Components of a 3D Laser Cutting System
Laser Source
The laser source is the heart of the system and is responsible for generating a beam with the required parameters. Key components include:
- Laser resonator.
- Power supply.
- Cooling system.
- Beam parameter control system.
- Monitoring and diagnostic systems.
Beam Delivery System
Depending on the laser type, the beam is delivered to the cutting head via:
- Mirror System (CO₂ Lasers): A system of precisely aligned mirrors reflecting the beam.
- Fiber Optic Cable (Fiber and Disk Lasers): Flexible optical fiber transporting the beam.
Cutting Head
An advanced 3D cutting head includes:
- Beam focusing system (lenses or mirrors).
- Distance control system from the material (capacitive or inductive).
- Nozzle for delivering assist gas.
- Cooling system.
- Process sensors (temperature, gas pressure).
- Anti-collision system.
Positioning System
The positioning system in 3D machines includes:
- Precision linear axis drives.
- Encoder-equipped motors for rotary axes.
- Position measurement systems.
- Advanced motion control algorithms.
- Calibration and error compensation systems.
Control Unit
Modern 3D cutting machine control systems feature:
- Industrial multi-core processors.
- Advanced CAD/CAM software.
- Collision prediction system.
- Intelligent path optimization algorithms.
- Interfaces for communication with production management systems.
Technological Process of 3D Laser Cutting
Data Preparation
The process begins with:
- Creating a 3D model of the component.
- Designing the cutting shapes.
- Generating tool paths.
- Cutting process simulation.
- Optimization of technological parameters.
Setting Process Parameters
Key parameters of 3D laser cutting include:
- Laser power (typically 1-6 kW for tubes and profiles).
- Feed rate (usually 1-10 m/min, depending on material and thickness).
- Beam focus (focus position relative to the surface).
- Selection of assist gas (oxygen, nitrogen, argon).
- Gas pressure (0.5-20 bar).
- Nozzle distance from material (0.5-2.0 mm).
Cutting Strategies
Various cutting strategies are used in 3D machining:
- Circular Cutting: The head moves around the profile, completing a full pass.
- Segment Cutting: The profile is divided into segments processed sequentially.
- Spiral Cutting: The cutting path follows a spiral around the profile.
- Adaptive Cutting: Parameters and paths are adjusted in real-time.
Quality Control
Modern 3D cutting systems integrate advanced quality control methods:
- Adaptive laser power control systems.
- Real-time process monitoring (thermal cameras, optical sensors).
- Defect detection systems.
- Geometric measurements of finished components.
- Process parameter documentation for repeatability.
Technical Challenges in 3D Laser Cutting
Geometric Precision
Ensuring high dimensional accuracy in 3D cutting requires addressing the following issues:
- Compensation for material thermal deformation.
- Accounting for material springback after cutting.
- Minimizing cutting kerf taper.
- Control of cut perpendicularity relative to the surface.
Thermal Issues
3D laser cutting presents the following thermal challenges:
- Uneven heating of profiles and tubes.
- Risk of overheating thin walls.
- Control of heat-affected zones in sensitive materials.
- Heat dissipation from the cutting area.
Material Challenges
The diversity of materials used in profile and tube manufacturing creates specific problems:
- Surface reflectivity of aluminum and copper alloys.
- Differences in energy absorption for various materials.
- Challenges in cutting composite and multi-layer materials.
- Edge quality control in materials with varying structures.
Latest Trends in 3D Laser Cutting Technology
Intelligent Control Systems
Modern 3D cutting machines are equipped with:
- Machine learning systems for parameter optimization.
- Adaptive process controllers with feedback loops.
- Advanced predictive diagnostics.
- Operator assistance systems based on augmented reality.
High-Power Lasers
Advances in laser sources enable:
- Machining of profiles with thicker walls.
- Increased cutting speeds.
- Improved edge quality.
- Expansion of the range of machinable materials.
Integration with Production Systems
Modern 3D cutting systems are part of broader production systems:
- Direct integration with production management systems.
- Automation of loading and unloading.
- Synchronization with subsequent machining steps.
- Full traceability and process documentation.
Summary
3D laser cutting technology represents a breakthrough in the machining of tubes, profiles, and special sections. Thanks to its ability to perform precise spatial machining, it enables the creation of complex shapes and connections that were previously difficult or impossible to achieve. The dynamic development of both laser sources and control systems makes this method increasingly efficient, precise, and cost-effective. However, technical challenges remain, particularly in machining reflective materials and process quality control, which are areas of intensive research and development.
«return