2025-02-15
Komponenty systemu spawania zrobotyzowanego: kompleksowy przegląd
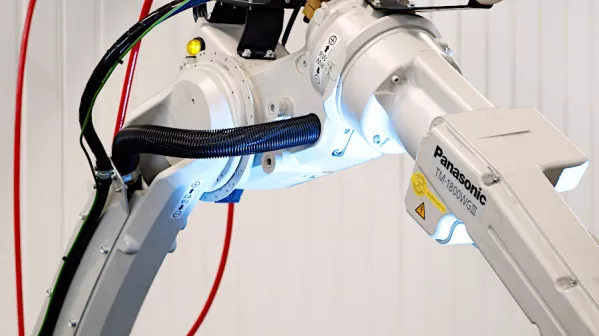
Spawanie zrobotyzowane stanowi obecnie kluczowy element nowoczesnych procesów produkcyjnych w wielu gałęziach przemysłu. Dynamiczny rozwój tej technologii przyczynia się do znaczącego wzrostu wydajności, jakości oraz bezpieczeństwa procesów spawalniczych. U podstaw efektywnego systemu spawania zrobotyzowanego leży odpowiednia konfiguracja jego komponentów, które wspólnie tworzą zintegrowane, precyzyjne i niezawodne stanowisko produkcyjne. Niniejszy artykuł przedstawia szczegółową analizę głównych elementów składowych systemów spawania zrobotyzowanego, ich specyfikę techniczną oraz wzajemne powiązania funkcjonalne.
1. Ramię robota i jego charakterystyka
1.1. Typy robotów stosowanych w spawaniu
W zastosowaniach spawalniczych wykorzystuje się przede wszystkim roboty o kinematyce szeregowej (antropomorficzne), które charakteryzują się dużą uniwersalnością i elastycznością. Najbardziej rozpowszechnione są konfiguracje 6-osiowe, umożliwiające pozycjonowanie narzędzia spawalniczego pod dowolnym kątem w przestrzeni roboczej. W specjalistycznych zastosowaniach spotyka się również:
- Roboty typu SCARA - stosowane głównie w spawaniu elementów płaskich
- Roboty o kinematyce równoległej - wykorzystywane w aplikacjach wymagających wysokiej dynamiki
- Roboty typu gantry - dedykowane do spawania konstrukcji wielkogabarytowych
1.2. Parametry techniczne ramion robotów spawalniczych
Kluczowe parametry robotów stosowanych w spawalnictwie obejmują:
- Udźwig - typowo w zakresie 6-210 kg (uwzględniając masę manipulatora spawalniczego)
- Zasięg roboczy - od 1,4 m dla małych aplikacji do ponad 3,5 m dla robotów wielkogabarytowych
- Powtarzalność pozycjonowania - na poziomie ±0,05-0,1 mm
- Liczba stopni swobody - najczęściej 6 osi, choć w zaawansowanych aplikacjach stosuje się również rozwiązania 7-osiowe
- Prędkość ruchu - osiągająca nawet 2 m/s dla szybkiego przemieszczania między punktami spawania
- Odporność na warunki środowiskowe - specjalne osłony chroniące przed rozpryskami i pyłem spawalniczym
1.3. Specjalizowane rozwiązania konstrukcyjne
W robotach spawalniczych stosuje się szereg specjalizowanych rozwiązań konstrukcyjnych:
- Prowadzenie przewodów zasilających i sterujących wewnątrz ramienia robota (hollow wrist)
- Specjalne powłoki ochronne odporne na rozpryski spawalnicze
- Systemy chłodzenia przegubów dla aplikacji o wysokim obciążeniu cieplnym
- Wzmocnione konstrukcje nadgarstka robota zapewniające stabilność podczas prowadzenia procesu spawania
2. Narzędzia spawalnicze
2.1. Palniki spawalnicze
Palniki stanowią kluczowy element interfejsu między robotem a procesem spawania. Można wyróżnić następujące typy palników:
2.1.1. Palniki MIG/MAG
- Konstrukcja chłodzona powietrzem (do 250-300 A)
- Konstrukcja chłodzona cieczą (do 500-600 A)
- Palniki z systemem automatycznego czyszczenia (TCP - Tool Center Point)
- Palniki z wbudowanymi sensorami (napięcia łuku, temperatury, przepływu gazu)
2.1.2. Palniki TIG
- Palniki standardowe z elektrodą wolframową
- Palniki z podawaniem drutu zimnego
- Palniki z systemem szybkiej wymiany elektrody
- Specjalistyczne palniki z chłodzonymi elektrodami dla wysokich natężeń prądu
2.1.3. Głowice do spawania laserowego
- Głowice z układami optycznymi do formowania wiązki
- Głowice hybrydowe (laser + MIG/MAG)
- Głowice z systemami skanującymi umożliwiającymi spawanie bez przemieszczania ramienia robota
2.2. Systemy podawania drutu
Precyzyjne i niezawodne podawanie materiału dodatkowego jest kluczowym elementem procesu spawania zrobotyzowanego. W tym obszarze wyróżniamy:
2.2.1. Podajniki drutu
- Podajniki push - z mechanizmem podającym umieszczonym przy szpuli z drutem
- Podajniki pull - z mechanizmem podającym umieszczonym przy palniku
- Systemy push-pull - zapewniające najlepszą kontrolę podawania na dużych odległościach
- Podajniki z napędem serwo zapewniające precyzyjną kontrolę prędkości podawania
2.2.2. Szpule i bębny z materiałem dodatkowym
- Standardowe szpule (5-18 kg)
- Bębny technologiczne (100-300 kg) dla produkcji wielkoseryjnej
- Systemy szybkiej wymiany szpul minimalizujące przestoje
2.2.3. Prowadniki drutu
- Pancerze prowadzące dostosowane do różnych typów materiałów (aluminium, stal, stopy specjalne)
- Systemy z rolkami prowadzącymi dla materiałów miękkich
- Specjalne prowadniki z niskim współczynnikiem tarcia dla drutów proszkowych
2.3. Uchwyty i systemy mocowania palników
Sposób mocowania palnika do ramienia robota ma istotny wpływ na precyzję procesu:
- Sztywne mocowania dla standardowych aplikacji
- Mocowania z elementami podatnymi kompensującymi niedokładności pozycjonowania
- Systemy szybkiej wymiany palnika (QCS - Quick Change System)
- Uchwyty z wbudowaną ochroną antykolizyjną
3. Systemy sterowania i programowania
3.1. Kontrolery robotów spawalniczych
Nowoczesne kontrolery robotów spawalniczych charakteryzują się:
- Zintegrowanym sterowaniem procesem spawania i ruchem robota
- Możliwością sterowania wieloma osiami zewnętrznymi (pozycjonery, tory jezdne)
- Zaawansowanymi algorytmami interpolacji ścieżki dla złożonych trajektorii
- Modułami bezpieczeństwa zgodnie z normami ISO/TS 15066
- Komunikacją z nadrzędnymi systemami produkcyjnymi (MES, ERP)
3.2. Źródła spawalnicze
Współczesne źródła prądu dla spawania zrobotyzowanego oferują:
- Cyfrowe sterowanie parametrami procesu z częstotliwością kilku kHz
- Zaawansowane tryby pracy (CMT - Cold Metal Transfer, pulsacja, AC MIG)
- Monitorowanie i rejestrację parametrów w czasie rzeczywistym
- Interfejsy komunikacyjne do integracji z kontrolerem robota (EtherNet/IP, Profibus, DeviceNet)
- Zaawansowane algorytmy adaptacyjne dostosowujące parametry do zmiennych warunków
3.3. Metody programowania
W zależności od specyfiki produkcji, stosuje się różne techniki programowania:
3.3.1. Programowanie online
- Teach-in - ręczne prowadzenie robota przez punkty trajektorii
- Programowanie przy użyciu panelu operatora (teach pendant)
- Programowanie z wykorzystaniem technik odwzorowania ruchu operatora
3.3.2. Programowanie offline
- Systemy CAD/CAM z modułami do generowania ścieżek robota
- Środowiska symulacyjne umożliwiające weryfikację programu przed wdrożeniem
- Automatyczne generowanie programów na podstawie modeli CAD spawanych elementów
- Optymalizacja ścieżek z uwzględnieniem dostępności, kolizji i parametrów technologicznych
3.3.3. Systemy hybrydowe
- Wstępne programowanie offline z dopracowaniem na stanowisku
- Programy parametryczne dostosowujące się do wariantów produktu
- Systemy z elementami uczenia maszynowego optymalizujące ścieżki na podstawie doświadczeń
4. Osprzęt pomocniczy
4.1. Pozycjonery i obrotniki
Elementy te umożliwiają optymalizację pozycji spawania i są kluczowe dla zapewnienia wysokiej jakości:
4.1.1. Typy pozycjonerów
- Jednoosiowe stoły obrotowe
- Dwuosiowe pozycjonery typu L
- Trzyosiowe pozycjonery zapewniające pełną kontrolę orientacji detalu
- Wielostanowiskowe pozycjonery z funkcją wymiany detali podczas pracy robota
4.1.2. Parametry techniczne
- Udźwig od kilkudziesięciu kg do nawet 20 ton dla dużych konstrukcji
- Powtarzalność pozycjonowania na poziomie ±0,1 mm
- Synchronizacja ruchu z robotem przez kontroler nadrzędny
- Prędkości obrotowe dostosowane do wymagań procesu (typowo 10-120 stopni/s)
4.2. Tory jezdne i systemy pozycjonowania robota
Dla aplikacji wymagających dużej przestrzeni roboczej stosuje się:
- Tory jezdne podłogowe - zwiększające obszar roboczy w osi poziomej
- Systemy portalowe - umożliwiające pozycjonowanie w trzech osiach
- Rozwiązania kolumnowe - pozwalające na obsługę wysokich konstrukcji
- Systemy mobilne - dla elastycznej rekonfiguracji stanowiska
4.3. Systemy mocowania detali
Precyzyjne i stabilne mocowanie elementów spawanych jest kluczowe dla jakości procesu:
- Przyrządy spawalnicze z kompensacją odkształceń termicznych
- Systemy pneumatyczne i hydrauliczne zapewniające powtarzalność mocowania
- Modułowe systemy szybkiego montażu
- Przyrządy z wbudowanymi elementami pozycjonującymi
- Systemy weryfikacji poprawności zamocowania (czujniki obecności, systemy wizyjne)
4.4. Systemy czyszczenia palnika
W celu zapewnienia nieprzerwanej pracy, stosuje się automatyczne stacje czyszczące:
- Mechaniczne systemy czyszczenia końcówki prądowej
- Frezy do usuwania nagaru i rozprysków
- Systemy natryskiwania środków antyadhezyjnych
- Kontrola geometrii końcówki palnika
- Automatyczne odcinanie drutu
5. Systemy sensoryczne i monitorowania procesu
5.1. Sensory do śledzenia złącza
Nowoczesne systemy spawania zrobotyzowanego wykorzystują różnorodne sensory do adaptacyjnego prowadzenia procesu:
5.1.1. Sensory łukowe
- Pomiar napięcia łuku w trakcie oscylacji palnika
- Detekcja krawędzi na podstawie zmian parametrów elektrycznych
- Systemy adaptacyjne dostosowujące parametry do zmiennej geometrii złącza
5.1.2. Sensory wizyjne
- Systemy laserowe do skanowania geometrii przed spawaniem
- Kamery 2D i 3D do śledzenia złącza w czasie rzeczywistym
- Systemy termowizyjne monitorujące rozkład temperatury
5.1.3. Sensory dotykowe
- Systemy wyszukiwania położenia elementów przez dotyk
- Pomiar geometrii złącza przez fizyczny kontakt
5.2. Systemy kontroli jakości online
Integralnym elementem zaawansowanych stanowisk są systemy monitorujące jakość w czasie rzeczywistym:
- Monitoring parametrów elektrycznych (napięcie, natężenie, stabilność łuku)
- Systemy wizyjne oceniające geometrię spoiny
- Systemy ultradźwiękowe do wykrywania wad wewnętrznych
- Zaawansowana analityka danych procesu z wykrywaniem anomalii
6. Integracja systemowa
6.1. Bezpieczeństwo stanowiska zrobotyzowanego
Stanowiska spawania zrobotyzowanego wymagają kompleksowych systemów bezpieczeństwa:
- Osłony stałe i ruchome ograniczające dostęp do strefy roboczej
- Kurtyny świetlne i skanery laserowe monitorujące przestrzeń
- Systemy zatrzymania awaryjnego
- Tryby pracy o ograniczonej prędkości podczas programowania
- Systemy zgodne z normami ISO 10218 i ISO/TS 15066
6.2. Systemy wyciągowe i filtracyjne
Efektywne odprowadzanie dymów spawalniczych jest kluczowe zarówno dla jakości procesu, jak i ochrony środowiska:
- Wyciągi miejscowe zintegrowane z palnikiem
- Centralne systemy filtracyjne z rekuperacją ciepła
- Systemy monitorowania jakości powietrza
- Filtry o różnej efektywności w zależności od rodzaju spawanych materiałów
6.3. Integracja z systemami produkcyjnymi
Nowoczesne stanowiska spawania zrobotyzowanego są elementem cyfrowego ekosystemu fabryki:
- Komunikacja z systemami MES (Manufacturing Execution System)
- Integracja z systemami zarządzania jakością
- Gromadzenie danych dla analityki Big Data
- Implementacja koncepcji Przemysłu 4.0 z wykorzystaniem IoT (Internet of Things)
- Cyfrowe bliźniaki procesów spawalniczych do predykcyjnego utrzymania ruchu
Zintegrowany ekosystem
Komponenty systemów spawania zrobotyzowanego tworzą złożony, zintegrowany ekosystem, którego efektywność zależy od właściwego doboru i konfiguracji każdego elementu. Nowoczesne rozwiązania charakteryzują się wysokim stopniem digitalizacji, adaptacyjności oraz zdolnością do integracji z nadrzędnymi systemami produkcyjnymi. Kluczowymi trendami rozwojowymi są: zwiększona autonomia systemów, zaawansowana sensoryka, implementacja elementów sztucznej inteligencji oraz kompleksowe podejście do kontroli jakości procesu. Właściwe zrozumienie specyfiki poszczególnych komponentów oraz ich wzajemnych powiązań jest niezbędne dla skutecznego projektowania, wdrażania i eksploatacji systemów spawania zrobotyzowanego w nowoczesnym środowisku produkcyjnym.
«powrót