2025-02-28
Technologia cięcia laserowego 3D - rewolucja w obróbce rur, profili i kształtowników specjalnych
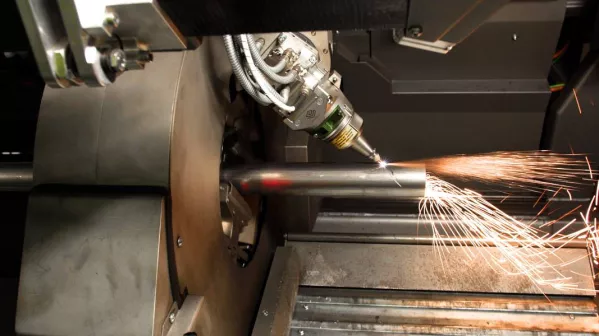
Cięcie laserowe 3D zrewolucjonizowało przemysł obróbki metali, wprowadzając nowy poziom precyzji, elastyczności i wydajności w produkcji elementów z rur, profili i kształtowników specjalnych. W przeciwieństwie do konwencjonalnych metod mechanicznych, technologia ta umożliwia wykonywanie skomplikowanych operacji cięcia bez konieczności stosowania wielu narzędzi i przeprowadzania licznych operacji technologicznych. Niniejszy artykuł przedstawia kompleksową analizę technologii cięcia laserowego 3D, jej zasad działania, typów stosowanych laserów oraz kluczowych aspektów technicznych związanych z tą innowacyjną metodą obróbki.
Zasady działania maszyn do cięcia przestrzennego
Podstawy fizyczne procesu
Cięcie laserowe 3D opiera się na wykorzystaniu skoncentrowanej wiązki światła o wysokiej energii, która powoduje miejscowe topienie, spalanie lub odparowywanie materiału w ściśle określonym obszarze. Proces ten inicjuje reakcję termiczną, podczas której materiał jest usuwany, tworząc precyzyjną szczelinę cięcia. Istotą technologii jest możliwość manipulowania wiązką laserową w trzech wymiarach, co pozwala na obróbkę obiektów przestrzennych, takich jak rury czy profile.
Kinematyka maszyn do cięcia 3D
Maszyny do cięcia laserowego 3D charakteryzują się złożoną kinematyką, która umożliwia precyzyjne prowadzenie głowicy laserowej wokół obrabianego przedmiotu. Wyróżniamy dwa główne typy systemów kinematycznych:
Systemy z ruchomą głowicą i obrotowym stołem:
- Przedmiot jest obracany wokół swojej osi podłużnej
- Głowica laserowa porusza się w osiach X, Y i Z
- Zintegrowane systemy obrotowe zapewniają dodatkową oś obrotu (B lub C)
- Umożliwiają obróbkę z dowolnego kierunku wokół elementu
Systemy z nieruchomą głowicą i wieloosiowym manipulatorem przedmiotu:
- Głowica laserowa pozostaje w stałej pozycji
- Element obrabiany jest manipulowany przez system z minimum 5 osiami swobody
- Zapewniają większą precyzję przy obróbce ciężkich elementów
- Lepiej sprawdzają się przy obróbce dużych kształtowników
Sterowanie procesem
Nowoczesne systemy do cięcia laserowego 3D wyposażone są w zaawansowane układy sterowania numerycznego (CNC), które odpowiadają za:
- Precyzyjne pozycjonowanie głowicy względem obrabianego profilu
- Kontrolę parametrów wiązki laserowej (moc, tryb pracy, fokus)
- Zarządzanie procesem chłodzenia
- Synchronizację ruchu osi obrotowych z liniowymi
- Adaptacyjną kontrolę procesu w czasie rzeczywistym
Kluczowym elementem jest zaawansowane oprogramowanie CAD/CAM, które umożliwia projektowanie złożonych kształtów i automatyczne generowanie ścieżek narzędzia. Systemy te często wyposażone są w moduły symulacji procesu cięcia, które pozwalają na wykrycie potencjalnych kolizji i optymalizację parametrów obróbki.
Różnice między cięciem laserowym 2D a 3D
Koncepcja wymiarowości w obróbce laserowej
Podstawowa różnica między systemami 2D i 3D dotyczy liczby osi, wzdłuż których przemieszcza się głowica tnąca oraz stopni swobody manipulacji przedmiotem:
Systemy 2D:
- Pracują w układzie dwóch osi kartezjańskich (X i Y)
- Przeznaczone są do cięcia płaskich materiałów (blachy, arkusze)
- Zazwyczaj posiadają stały fokus wiązki lub ograniczoną regulację w osi Z
Systemy 3D:
- Operują w układzie minimum pięciu osi
- Umożliwiają obróbkę powierzchni zakrzywionych i elementów przestrzennych
- Zapewniają możliwość ustawienia głowicy pod dowolnym kątem względem obrabianej powierzchni
Złożoność obróbki
Cięcie laserowe 3D charakteryzuje się znacznie większą złożonością technologiczną:
Wymogi geometryczne:
- Konieczność ciągłej kontroli odległości dyszy od powierzchni elementu
- Utrzymanie optymalnego kąta padania wiązki na powierzchnię
- Kompensacja geometryczna dla zakrzywionych powierzchni
Wyzwania procesowe:
- Zmienne warunki odprowadzania ciepła w zależności od geometrii
- Konieczność adaptacji parametrów w czasie rzeczywistym
- Ryzyko uszkodzenia przeciwległej ścianki profilu lub rury
Aspekty programowania:
- Złożone algorytmy generowania ścieżek
- Wieloetapowe planowanie procesu
- Zaawansowana wizualizacja i weryfikacja programu
Zastosowania specjalistyczne
Cięcie laserowe 3D otwiera nowe możliwości w zakresie:
- Wykonywania połączeń typu "jigsaw" w konstrukcjach rurowych
- Realizacji złożonych otworów technologicznych i ozdobnych
- Przygotowania precyzyjnych zakończeń elementów do późniejszego spawania
- Wykonywania wycięć pod kątem innym niż prosty do powierzchni profilu
- Obróbki elementów o zmiennej geometrii przekroju
Typy laserów używanych do obróbki metali
Lasery CO₂
Lasery CO₂ wykorzystują mieszaninę gazów (dwutlenek węgla, azot, hel) jako ośrodek czynny. Generują wiązkę o długości fali 10,6 μm, która znajduje się w zakresie podczerwieni.
Charakterystyka:
- Moc: od 1,5 kW do 20 kW
- Wydajność energetyczna: 8-10%
- Jakość wiązki: wysoka, szczególnie dla niższych mocy
- Koszty eksploatacyjne: umiarkowane, głównie związane z wymianą gazów i zwierciadłek
Zalety w cięciu 3D:
- Doskonała jakość krawędzi przy cięciu stali węglowych i niskostopowych
- Możliwość uzyskania wąskiej szczeliny cięcia
- Dobra absorpcja przez większość materiałów konstrukcyjnych
Ograniczenia:
- Niższa wydajność przy cięciu materiałów refleksyjnych (aluminium, miedź)
- Konieczność stosowania złożonych układów optycznych z ruchomymi zwierciadłami
- Ograniczona możliwość miniaturyzacji układu optycznego
Lasery światłowodowe (fiber)
Lasery światłowodowe wykorzystują włókno szklane domieszkowane pierwiastkami ziem rzadkich (najczęściej iterbem) jako ośrodek czynny. Generują wiązkę o długości fali około 1,07 μm.
Charakterystyka:
- Moc: od 1 kW do 30 kW
- Wydajność energetyczna: 25-35%
- Jakość wiązki: bardzo wysoka, zachowana nawet przy wysokich mocach
- Koszty eksploatacyjne: niskie, minimalna konserwacja
Zalety w cięciu 3D:
- Wyższa absorpcja przez metale, szczególnie refleksyjne
- Możliwość transportu wiązki światłowodem do głowicy tnącej
- Doskonałe parametry cięcia cienkich materiałów
- Wysoka wydajność energetyczna
Ograniczenia:
- Wyższe koszty początkowe
- Większe ryzyko przebicia przy cięciu rur o małych średnicach
Lasery dyskowe
Lasery dyskowe wykorzystują cienki dysk krystaliczny (najczęściej Yb:YAG) jako ośrodek aktywny. Generują wiązkę o długości fali około 1,03 μm.
Charakterystyka:
- Moc: od 1 kW do 16 kW
- Wydajność energetyczna: 15-25%
- Jakość wiązki: niezwykle wysoka, niezależna od mocy wyjściowej
- Koszty eksploatacyjne: średnie, wyższe niż w laserach światłowodowych
Zalety w cięciu 3D:
- Najwyższa jakość wiązki przy dużych mocach
- Doskonała koncentracja energii
- Możliwość precyzyjnej obróbki grubszych materiałów
Ograniczenia:
- Złożona konstrukcja układu optycznego
- Wyższe koszty zakupu i utrzymania
- Mniejsza dostępność na rynku
Porównanie technologii laserowych w zastosowaniach do cięcia 3D:
Długość fali:
- Laser CO₂: 10,6 μm
- Laser światłowodowy: 1,07 μm
- Laser dyskowy: 1,03 μm
Absorpcja przez stal:
- Laser CO₂: Dobra
- Laser światłowodowy: Bardzo dobra
- Laser dyskowy: Bardzo dobra
Absorpcja przez aluminium:
- Laser CO₂: Słaba
- Laser światłowodowy: Dobra
- Laser dyskowy: Dobra
Maksymalna grubość cięcia (stal):
- Laser CO₂: 25 mm
- Laser światłowodowy: 30 mm
- Laser dyskowy: 35 mm
Jakość krawędzi:
- Laser CO₂: Bardzo dobra
- Laser światłowodowy: Dobra
- Laser dyskowy: Bardzo dobra
Prędkość cięcia cienkich materiałów:
- Laser CO₂: Umiarkowana
- Laser światłowodowy: Wysoka
- Laser dyskowy: Wysoka
Elastyczność systemu:
- Laser CO₂: Ograniczona
- Laser światłowodowy: Bardzo wysoka
- Laser dyskowy: Wysoka
Koszt zakupu:
- Laser CO₂: Niski/średni
- Laser światłowodowy: Średni/wysoki
- Laser dyskowy: Wysoki
Koszty eksploatacji:
- Laser CO₂: Średnie
- Laser światłowodowy: Niskie
- Laser dyskowy: Średnie
Zapotrzebowanie na energię:
- Laser CO₂: Wysokie
- Laser światłowodowy: Niskie
- Laser dyskowy: Średnie
Komponenty systemu do cięcia laserowego 3D
Źródło laserowe
Źródło laserowe stanowi serce systemu i odpowiada za generowanie wiązki o odpowiednich parametrach. Kluczowe elementy to:
- Rezonator laserowy
- Układ zasilania
- System chłodzenia
- Układ sterowania parametrami wiązki
- Systemy monitorowania i diagnostyki
Układ transportu wiązki
W zależności od typu lasera, wiązka transportowana jest do głowicy tnącej za pomocą:
- Układu zwierciadłek (lasery CO₂) - system precyzyjnie ustawionych zwierciadeł odbijających wiązkę
- Światłowodu (lasery fiber i dyskowe) - elastyczne włókno optyczne transportujące wiązkę
Głowica tnąca
Zaawansowana głowica do cięcia 3D zawiera:
- Układ ogniskujący wiązkę (soczewki lub zwierciadła)
- System kontroli odległości od materiału (pojemnościowy lub indukcyjny)
- Dyszę doprowadzającą gaz technologiczny
- Układ chłodzenia
- Sensory procesowe (temperatura, ciśnienie gazu)
- System anty-kolizyjny
System pozycjonowania
System pozycjonowania w maszynach 3D obejmuje:
- Precyzyjne napędy osi liniowych
- Silniki z enkoderem do napędu osi obrotowych
- Układy pomiarowe pozycji
- Zaawansowane algorytmy sterowania ruchem
- Systemy kalibracji i kompensacji błędów
Jednostka sterująca
Nowoczesne systemy sterowania maszynami do cięcia 3D charakteryzują się:
- Wielordzeniowymi procesorami przemysłowymi
- Zaawansowanym oprogramowaniem CAD/CAM
- Systemem predykcji kolizji
- Inteligentnymi algorytmami optymalizacji ścieżki
- Interfejsami do komunikacji z systemami zarządzania produkcją
Proces technologiczny cięcia laserowego 3D
Przygotowanie danych
Proces rozpoczyna się od:
- Przygotowania modelu 3D obrabianego elementu
- Zaprojektowania kształtów cięcia
- Wygenerowania ścieżek narzędzia
- Symulacji procesu cięcia
- Optymalizacji parametrów technologicznych
Ustawienie parametrów procesowych
Kluczowe parametry cięcia laserowego 3D obejmują:
- Moc lasera (typowo 1-6 kW dla rur i profili)
- Prędkość posuwu (zazwyczaj 1-10 m/min, zależnie od materiału i grubości)
- Ogniskowanie wiązki (pozycja ogniska względem powierzchni)
- Dobór gazu wspomagającego (tlen, azot, argon)
- Ciśnienie gazu (0,5-20 bar)
- Odstęp dyszy od materiału (0,5-2,0 mm)
Strategie cięcia
W obróbce 3D stosuje się różne strategie cięcia:
- Cięcie pierścieniowe - głowica porusza się wokół profilu, wykonując pełne przejście
- Cięcie segmentowe - profil jest dzielony na segmenty, które są obrabiane sekwencyjnie
- Cięcie spiralne - ścieżka cięcia ma kształt spirali owijającej się wokół profilu
- Cięcie adaptacyjne - parametry i ścieżka dostosowywane są w czasie rzeczywistym
Kontrola jakości
Nowoczesne systemy cięcia 3D integrują zaawansowane metody kontroli jakości:
- Adaptacyjne systemy kontroli mocy lasera
- Monitoring procesu w czasie rzeczywistym (kamery termowizyjne, sensory świetlne)
- Systemy wykrywania wad cięcia
- Pomiary geometryczne gotowych elementów
- Dokumentacja parametrów procesu dla zapewnienia powtarzalności
Wyzwania techniczne w cięciu laserowym 3D
Precyzja geometryczna
Zapewnienie wysokiej dokładności wymiarowej w cięciu 3D wymaga rozwiązania następujących problemów:
- Kompensacja deformacji termicznych materiału
- Uwzględnienie sprężynowania materiału po cięciu
- Minimalizacja stożkowatości szczeliny cięcia
- Kontrola prostopadłości cięcia względem powierzchni
Problemy termiczne
Cięcie laserowe 3D wiąże się z następującymi wyzwaniami termicznymi:
- Nierównomierne nagrzewanie się profili i rur
- Ryzyko przegrzania cienkich ścianek
- Kontrola strefy wpływu ciepła w materiałach wrażliwych
- Odprowadzanie ciepła z miejsca cięcia
Wyzwania materiałowe
Różnorodność materiałów stosowanych w produkcji profili i rur stwarza specyficzne problemy:
- Refleksyjność powierzchni stopów aluminium i miedzi
- Różnice w absorpcji energii dla różnych materiałów
- Problemy z cięciem materiałów kompozytowych i wielowarstwowych
- Kontrola jakości krawędzi w materiałach o różnej strukturze
Najnowsze trendy w technologii cięcia laserowego 3D
Inteligentne systemy sterowania
Współczesne maszyny do cięcia 3D wyposażane są w:
- Systemy uczenia maszynowego do optymalizacji parametrów
- Adaptacyjne kontrolery procesu z pętlą sprzężenia zwrotnego
- Zaawansowaną diagnostykę predykcyjną
- Systemy wspomagania operatora oparte na rozszerzonej rzeczywistości
Lasery wysokiej mocy
Rozwój źródeł laserowych pozwala na:
- Obróbkę profili o większych grubościach ścianek
- Zwiększenie prędkości cięcia
- Poprawę jakości krawędzi
- Rozszerzenie gamy obrabianych materiałów
Integracja z systemami produkcyjnymi
Nowoczesne systemy cięcia 3D stanowią element szerszych systemów produkcyjnych:
- Bezpośrednia integracja z systemami zarządzania produkcją
- Automatyzacja załadunku i rozładunku
- Synchronizacja z kolejnymi etapami obróbki
- Pełna identyfikowalność i dokumentacja procesu
Podsumowanie
Technologia cięcia laserowego 3D stanowi przełom w obróbce rur, profili i kształtowników specjalnych. Dzięki możliwości precyzyjnej obróbki przestrzennej, pozwala na realizację złożonych kształtów i połączeń, które wcześniej były trudne lub niemożliwe do wykonania. Dynamiczny rozwój zarówno źródeł laserowych, jak i systemów sterowania, sprawia, że metoda ta staje się coraz bardziej wydajna, precyzyjna i ekonomiczna. Jednocześnie wciąż istnieją wyzwania techniczne, szczególnie w zakresie obróbki materiałów refleksyjnych oraz kontroli jakości procesu, które stanowią obszar intensywnych badań i rozwoju.
«powrót